Macksteel
Metal Fabricator Eliminates Lacerations Due To Manually Stretch-Wrapping Sharp Parts
By Andy Brizek
As Featured In Industrial Hygiene News
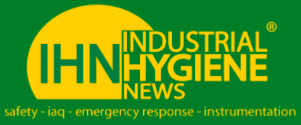
Charlie Mack stopped in his tracks at what he witnessed upon entering his packaging department. Two workers were struggling to hand-wrap plastic film around a palletload of sharp, laser cut, metal parts, passing the film roll back and forth over and under the pallet – while it was raised up on a forklift. As general manager for the metal products fabricator and distributor Macksteel, Watertown, South Dakota, Mack had finally had enough. Though this manual shrink-wrapping process is standard procedure at many metal shops, it’s also responsible for a large number of workplace injuries. At Macksteel, workplace injuries resulting in time lost from work occurred approximately every three months with direct costs averaging $2,000.00 per incident. Noting that most of these injuries were punctures, abrasions and lacerations to the arms due to contact with the sharp, metal parts that occurred during the manual wrapping process, Mack had grown increasingly concerned about the process and set out to find a safer, more efficient and effective way to manage packaging and shipping. “People tend to focus on the cost savings involved in avoiding injuries but there’s also a moral responsibility to provide a workplace that’s as safe as possible,” says Mack. “This particular job always gnawed at me because nobody had a better, safer way to do it, as far as we knew.”
Having previously identified safety trouble spots throughout the plant and investing in automated bending, cleaning and finishing equipment that successfully reduced the potential for injuries, Mack began searching for an automated solution to the wrapping process, and came across the TAB Wrapper Tornado. Designed and manufactured by TAB Industries in its Reading, PA, headquarters, the TAB Wrapper Tornado is a patent-pending, semi-automatic, orbital stretch-wrapping machine that wraps the plastic film 360 degrees around and under the pallet to attach the load to its pallet and keep it securely in place for transport. Instead of requiring workers to wrap the pallet while stooping under a 2,000-pound load, the forklift operator drives up to the machine until the pallet enters the wrapping ring then presses the start button. The TAB Wrapper then automatically wraps layers of plastic film around the palletized load, encasing the parts in a sturdy, unitized, weather-resistant load ready for transport to the customer or for storage. Mack purchased a TAB Wrapper and installed it in the packaging area, fitting neatly within the standard, nine-foot beam opening in the pallet rack system. Since replacing the manual process in 2012 with the TAB Wrapper, the company hasn’t had a single injury in the packaging department. “We just don’t get those cuts anymore and everyone feels better about doing the job right,” says Mack. “When you can take a task that nobody wants to do and make it safer and easier, it goes a long way towards building a culture of safety.”
When TAB Industries introduced its automated model last year with additional safety features, Mack quickly upgraded, selling his original TAB Wrapper to another metal fabricator. The new model features an automated cut and wrap device with a wireless remote control that enables the forklift operators to perform the entire wrapping process without leaving the seat. The potential for human contact with any of the thousands of laser-cut parts produced each week has been eliminated. “All my drivers love using it,” says Mack. “When other fab shop owners come in to see how we wrap our parts now, their jaws just drop.”
_____________________________________________________________________________
In financial terms, Mack has saved upwards of $5,000.00 per year simply by avoiding workers’ compensation claims and his insurance rates have dropped. Improving the wrapping quality has also led to savings. Workers occasionally used extra plastic film to make sure the load was secure, or worse, under-wrapped, thinking the load was secure when it really was not secure, leading to product damage due to shifting in transit. With two or three pallet loads returned out of an average of 900 pallets per month, with an average value of $1,500.00 per pallet load, packaging failures had cost approximately $50,000.00 per year. Using the TAB Wrapper has eliminated this type of product damage, along with the costly returns.
_____________________________________________________________________________
In terms of productivity, the TAB Wrapper allows a pallet to be wrapped by one person in 15 seconds versus the manual method, which took two people five minutes per pallet. This newly found time has allowed the packaging staff to meet their deadlines with less pressure, which contributes directly to a clean, organized work environment and to a culture of safety. “I consider the TAB Wrapper to be the industry’s best practice,” says Mack, “It allows us to work safer and faster, and it just plain works.”
After purchasing the automated equipment as part of the safety initiative, Mack invited a professional safety consultant from OSHA’S Safety & Health Achievement Recognition Program (SHARP) to tour the facility, assess progress and recommend areas of improvement. The consultant performed a mock OSHA inspection and recommended a series of adjustments such as upgrading railings and increasing the number of carbon monoxide monitors. “The consultant liked how the TAB Wrapper transformed a dangerous job into one of the safest in the plant,” says Mack, who is currently in the process of earning the SHARP certification. The certification recognizes companies as models of worksite safety and health.