Ta Chen
Stainless Steel Distributor Protects Valuable Fittings, Speeds Packaging and Cuts Costs with New Orbital Wrapping Machine
As Seen In Modern Metals
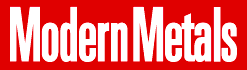
Bob Hunter felt a hint of apprehension almost every time he shipped an order out to a customer. As branch manager for Ta Chen International’s Houston, Texas operations, he manages the comings and goings of more than 1 million pounds of stainless steel per day for the master distributor of stainless, aluminum and nickel alloy coils, sheets, plates, long products, tubes and fittings. While all non-ferrous metals face a variety of risks during transport from exposure to weather and rust to careless handling and failed packaging, any one of which could cause enough damage to cause the shipment to be rejected, moving stainless steel fittings over the road carries additional risk. The high-grade metal is typically specified in sanitary and corrosive environments where even a single scratch renders the product useless. It is also subject to contamination from contact with many types of steel or iron that also renders the product useless. A single rejected shipment could cost the company upwards of tens of thousands of dollars, according to Hunter. “It’s critical for our customers that every product arrives on spec, secure and intact,” says Hunter, “so we’ve always had to take extra precautions to prevent any damage.”
Extra Precautions
Until recently, orders were picked from the warehouse, set on a wooden pallet and wrapped in plastic, either manually or using a semi-automatic, turntable stretch-wrapping machine. Two workers typically spent two to three minutes per pallet load wrapping each carton to the other cartons. But securing them to the pallet proved difficult. “The machine couldn’t wrap the load to the pallet so we would try it by hand and use a huge amount of extra plastic film just in case,” says Hunter. In many cases, metal or plastic banding was also used for extra confidence and security. Unfortunately, the plastic banding often popped loose in transit and the metal banding occasionally tore through the corrugated packaging, putting the product at risk of damage and contamination. Thanks to the extra precautions, Hunter enjoyed a high rate of customer satisfaction and rarely encountered a rejected shipment. In fact, Hunter didn’t realize he had a problem until he toured another metalworking company’s plant and saw how easily they handled their shipments. “I watched their forklift drivers take the loaded pallets to a new kind of orbital wrapping machine and it was wrapping the entire load to the pallet automatically while the pallet was still on the forklift,” recalls Hunter. “They loved it, they showed me how easy it is to operate and I had to have one for our plant.”
Efficiency By Design
The new kind of machine Hunter saw in action is called the TAB WRAPPER TORNADO. Designed and manufactured by the metal fabrication, warehousing and logistics company TAB Industries, LLC at its Reading, Pennsylvania headquarters, the orbital wrapping machine automatically wraps plastic stretch film 360 degrees around and under an entire pallet load to create a single, unitized, secure load. Completely encasing the packaged products in multiple layers of plastic, the packaging machine protects the cartons from exposure to the elements, ensures they stay in place and intact during warehousing and transportation and instills confidence that everything will arrive safely at its destination without risk of damage or contamination. “Andy [Brizek] let us test one for a week in our plant so we setup an experiment with one of our most difficult products,” says Hunter, referring to a very large, stainless fitting that had required both wrapping in plastic and metal banding to ship. To simulate typical shipping conditions, the test involved loading 400 lbs. of the fittings on a pallet, raising it on the forklift, wrapping it in the TAB WRAPPER TORNADO, then rotating it completely upside down – and bouncing it up and down. “No matter what we tried, the load stayed intact – the TAB WRAPPER amazed us,” says Hunter. “We knew that if it could handle these fittings then it could handle anything we need to pack and ship and we were sold.”
Hunter purchased the 80-inch TAB WRAPPER TORNADO, the middle size of three standard models. The 80-inch model accommodates a 48″ x 48″ skid loaded with cartons or loose products or both, even in different shapes and sizes. It can wrap long products such as beams, bars and channels of an infinite length, theoretically, since the wrapping ring remains stationary while the product is fed through the wrapper, on a conveyor, for example. The company also offers to custom design and manufacture the machine to nearly any size and recently built a 115-inch machine.
Immediate Results
For Hunter, the 80-inch model wraps 40 to 50 pallet loads per day. It has eliminated the need for manual wrapping, made the turntable wrapper obsolete and cut the time involved in wrapping each pallet load from a two to three minute scramble to 30 seconds while allowing one person to handle the whole process instead of needing two people. It has also eliminated the need for banding, which amounts to thousands of dollars annually, according to Hunter, and eliminated the time and labor involved in applying the banding, as well as in purchasing and maintaining inventory. The amount of plastic film needed has also been cut since the overwrapping “just in case” and other extra precautions are no longer needed. “Financially, the TAB WRAPPER paid for itself in a little more than a year,” says Hunter, “But most importantly, it does an outstanding job securing our product to the pallet, we haven’t had any packaging issues and it has really made our lives easier.”
The TAB WRAPPER is easy enough to operate that any of his 40 workers can safely use it after one day of training. Multiple emergency stops, automatic power shutoff, and ample, steel machine guarding are among the designed-in safeguards. Since the plastic film is replaced from a side access door, no one ever needs to climb into the machine. “We’ve had zero problems and zero downtime with this machine,” says Hunter. “Now, it’s so much easier to ship out an order, I feel good when a pallet goes on the truck and our customers appreciate it, too.” In fact, several customers, upon receiving the wrapped pallets, asked about the TAB WRAPPER and purchased their own. “If you wrap pallet loads in any kind of volume, I’d recommend taking a look at the TAB WRAPPER,” adds Hunter. “It’s a phenomenal piece of equipment.”
For more information on the TAB WRAPPER TORNADO, call Andy Brizek at TAB Industries, LLC, 610-921-0012 or see www.TABWRAPPER.com.